Tank Jacking System we offer consist of AGW1-U, EGW-V/D that work with our Hydraulic tank jacking systems to automatically weld the vertical and horizontal tank seams.
Tank jack up system leaflet 11.16.2022
Tank Jacking | Hydraulic Tank Jacks are a system of dual-stage hydraulic cylinders to lift and horizontally build storage tanks from the top down (the return trip needs external force or dead load for returning). This enables the horizontal and vertical welding of tank shell can be conducted on the ground efficiently and safely, cooperated with submerged-arc automatic girth welding machines (AGW) and vertical welding machines (EGW).
Hydraulic jacking system with the flexibility to lift storage tanks of different capacities and weights that are compatible to various manual or automatic welding methods adopted by tank contractors across the globe.
We can handle the largest tank projects and we can do it safety with maximum saving of time.
Our jacks are mounted securely on the floor and using the massive cylinder as a beam, will support the structure even in higher wind loads.
Each HLD jacking module has it’s own hydraulic pump and reservoir. They are linked to a central control that commands all aspects of the jacking operation.
Each standard HLD jacking module with 2 cylinders is capable of lifting 50,000 kg, which allows fewer jacks to raise a tank, it is designed with a large clearance from the tank shell that gives the workers extra room to quickly insert plates.
In operation, the cylinders are attached to the wall, the control loads the jack manually, or automatously via the addition of a PLC unit, then lift the structure holding tolerance within 2mm.
- High quality, dual-stage hydraulic cylinders to lift and horizontally build storage tanks from the top down (the return trip needs external force or dead load for returning). This enables the horizontal and vertical welding of tank shell can be conducted on the ground efficiently and safely, cooperated with submerged-arc automatic girth welding machines (AGW) and vertical welding machines (EGW).
- Specifications:
- Capacity of storage tank jacking module is 25t
- If appropriate quantity of modules are equipped, their storage jacking capacity can be up to 1500t
- “One for five” oil supply method: every set of hydraulic power units are connected to 5 sets of hydraulic cylinders, avoiding the disadvantages of traditional centralized oil supply (too many oil pipes and too many oil leakage points, ensuring to minimize the environmental pollution)
- Applications:
- Inverse installation construction of petrochemical vertical cylinder type steel tank (hydraulic lifting method)
- Steel liner inverse installation construction of power plant chimney
- Vertical hoisting and lifting of super large objects
- Main components
- 5X customized hydraulic cylinder
- Hydraulic power unit
- May supplement: centralized control operation box and power operation box
- Technical parameters
Model YT25-2700
Jacking capacity KN Max. 250
Lift stroke mm Max. 2700
Working pressure Mpa 20
Jacking speed mm/min 223
Ambient temperature °C -10-60
EGW -V/D: (Electrogas Welder) inverse installation electrogas (arc) welding machine, for jacking construction of storage tank; which is also know as a (AVW) automatic vert welder.
EGW (electrogas (arc) welding machines) which is also know as a (AVW) automatic vert welder are high efficient automatic welding equipment which achieves closed-loop control of carriage lifting via current feedback; Welding joint one-step forming thickness is 50mm, mainly used for thick plate single pass vertical seam welding in petroleum, chemical, blast furnace and ship building industries.
A standard EGW-V electro gas welder can with a single or double sided frame (recommended) to house all the necessary components along with the operators for high deposition code quality vertical welding operation in any part of the storage tank.
Vertical Welders Features
- Adopts EGW (Electro Gas Welding) process for high speed carbon steel vertical welding with FCAW (Flux Cored Arc Welding) Process option for alloy steel vertical welding
- Lightweight travel carriage, self-propelled, weatherproof, fully contained operators cabin which allows safe access to the weld joint and easy set up and install
- Lightweight Aluminum track, quick mount electro magnets , easy assembly and disassembly;
- Real time monitoring of arc and automatic control of weld pool level, welding gun position and automatic adjustment of electrical stick out;
- Sequence control in “Auto mode” to allow one button startup.
- Onboard- self-contained continuous water cooling system
- Fully integrated with LINCOLN electric welding systems as standard (other welding systems on client’s request)
- SEW drive system for reliable and steady travel
- Different standard configurations for site erected Bottom Up and Top Down erected storage tanks or heavy wall cylindrical structures (eg. towers, blast furnace).
Specifications:
- Welding seam forced water cooling, one-step forming
- Automatic control of molten pool liquid level, automatic adjustment of welding wire extension length
- Aluminum track, magnet adsorption, easy assembly and disassembly
- Small carriage volume, light weight, module structure
Technical parameters:
- Electrogas(arc) welding: Solid wire with gas shielding or inner shield wire
- Applicable tank diameter: ≥4.5m
- Applicable plate width: 1.6-3.2m (upward installation) 1.8-2.6m (inverse installation, Tank Jack up)
- Applicable plate thickness: 8-50mm
- Automatic welding speed: 0-250mm/min
- Vehicle rapid traveling speed: 550mm/min
Please go to the below link to get an idea of how our EGW system operates welding on 1” plate, that is 108” long onsite in Australia.
- https://www.youtube.com/watch?v=lwSXkONvMU4
AGW 1-U is a universal standard single sided Flat Bottom Tank Automatic Girth Welder (AGW) 3 O’clock welder Submerged arc automatic girth welding machines (AGW) is the machine used to automatic weld the circumferential weld inside and outside of vertical storage tank. This AGW 1-U can also be used for standard bottom up or top down tank Jack-UP construction.
Standard AGW characteristics:
- Standard configuration of the automatic girth welding machines the is reliable LINCOLN welding system
- Dual AC variable frequency motor drive ensures that the welding machine could walk along the storage tank stably within a certain speed range
- The machine head is equipped with welding seam automatic tracking system to keep the welding gun position accurately in the weld seam during the welding process.
- Powerful vacuum pump mounted in the middle part of the AGW frame to provide an effective flux recovery and recycling system.
- Additional flux holding mechanism has been added just above the welding head and flux belt to provide a more consent flow of flux to the welding process.
- The welding machine could be operated conveniently and clearly via the integrated control panel
- Available in single sided and double sided models for performing double and single side welding of liquefied petroleum gas, liquefied natural gas tanks
Girth Welders Features
- Fully integrated with LINCOLN electric submerged arc welding systems as standard (other welding systems on client’s request).
- Twin SEW motors drive system for reliable and steady weld travel .
- Inverter control for accurate speed adjustment.
- Fully adjustable weld head/ flux belt assembly.
- Precision machined slides ensure correct weld placement.
- Laser pointer to ensure correct tracking of the weld head in the circumferential seam.
- Powerful, reliable and efficient blower type vacuum flux recovery system.
- Flux heater option to keep flux away from moisture.
- Sequence control in “Auto mode” to allow one button startup.
- Integrated control with cooling for reliable operation in high temperature environment.
- Ergonomically positioned for the operator.
Applications:
- Traditional oil & water tank welding
- Tank Jack up type erection with below AGW track travel system
- Submerged arc welding (single-wire or twin-wire welding)
Technical parameters:
- Applicable tank diameter: 4.5m and above
- Applicable plate thickness: 8-45mm
- Applicable plate width: 1.8-3.2m (for bottom up tank shell plate erection) and 1.8-2.6m (Tank Jack up erection)
- Applicable steel grade: Carbon steel, low alloy steel, high strength steel
- Rack speed range: 100-2650mm/min
Optional AGW equipment:
- MPS (mobile power source, diesel welding machine) available for single or double sided welding
- Electric winch with arm mounted on top of AGW frame for lifting flux and wire from ground level to the working levels of the AGW
- Flux hopper heating element
- Automatic girth weld seam buffing attachment
- Intercom for the double sided AGW II
Tank Jacking | Hydraulic Tank Jacks are a system of dual-stage hydraulic cylinders to lift and horizontally build storage tanks from the top down (the return trip needs external force or dead load for returning). This enables the horizontal and vertical welding of tank shell can be conducted on the ground efficiently and safely, cooperated with submerged-arc automatic girth welding machines (AGW) and vertical welding machines (EGW).
Hydraulic jacking system with the flexibility to lift storage tanks of different capacities and weights that are compatible to various manual or automatic welding methods adopted by tank contractors across the globe.
We can handle the largest tank projects and we can do it safety with maximum saving of time.
Our jacks are mounted securely on the floor and using the massive cylinder as a beam, will support the structure even in higher wind loads.
Each HLD jacking module has it’s own hydraulic pump and reservoir. They are linked to a central control that commands all aspects of the jacking operation.
Each standard HLD jacking module with 2 cylinders is capable of lifting 50,000 kg, which allows fewer jacks to raise a tank, it is designed with a large clearance from the tank shell that gives the workers extra room to quickly insert plates.
In operation, the cylinders are attached to the wall, the control loads the jack manually, or automatously via the addition of a PLC unit, then lift the structure holding tolerance within 2mm.
- High quality, dual-stage hydraulic cylinders to lift and horizontally build storage tanks from the top down (the return trip needs external force or dead load for returning). This enables the horizontal and vertical welding of tank shell can be conducted on the ground efficiently and safely, cooperated with submerged-arc automatic girth welding machines (AGW) and vertical welding machines (EGW).
- Specifications:
- Capacity of storage tank jacking module is 25t
- If appropriate quantity of modules are equipped, their storage jacking capacity can be up to 1500t
- “One for five” oil supply method: every set of hydraulic power units are connected to 5 sets of hydraulic cylinders, avoiding the disadvantages of traditional centralized oil supply (too many oil pipes and too many oil leakage points, ensuring to minimize the environmental pollution)
- Applications:
- Inverse installation construction of petrochemical vertical cylinder type steel tank (hydraulic lifting method)
- Steel liner inverse installation construction of power plant chimney
- Vertical hoisting and lifting of super large objects
- Main components
- 5X customized hydraulic cylinder
- Hydraulic power unit
- May supplement: centralized control operation box and power operation box
- Technical parameters
Model YT25-2700
Jacking capacity KN Max. 250
Lift stroke mm Max. 2700
Working pressure Mpa 20
Jacking speed mm/min 223
Ambient temperature °C -10-60

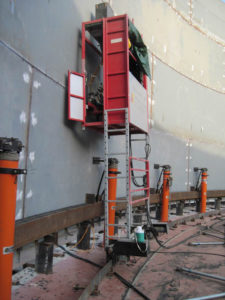
Tank Welding LLC.
Is your complete source for Automatic Storage Tank Welding Machines. We specialize in custom built to order automatic tank welding machines for LNG & flat bottom tanks. We have multiple Automatic Girth Welder designs (AGW) 3 O’clock Welder designs. EGW (Electrogas Welder), VUP & AVW Automatic Vert Welders, Vert Buggy, Tank Jacking systems, automatic Sphere welders. This line of equipment is built with your choice of USA made Lincoln or Miller welding systems. Our AGW travel is powered by top of the line twin German engineered inverter controlled drive motors.
Explore all of our merchandise and contact us by phone or email. http://tankwelding.com/about-us/